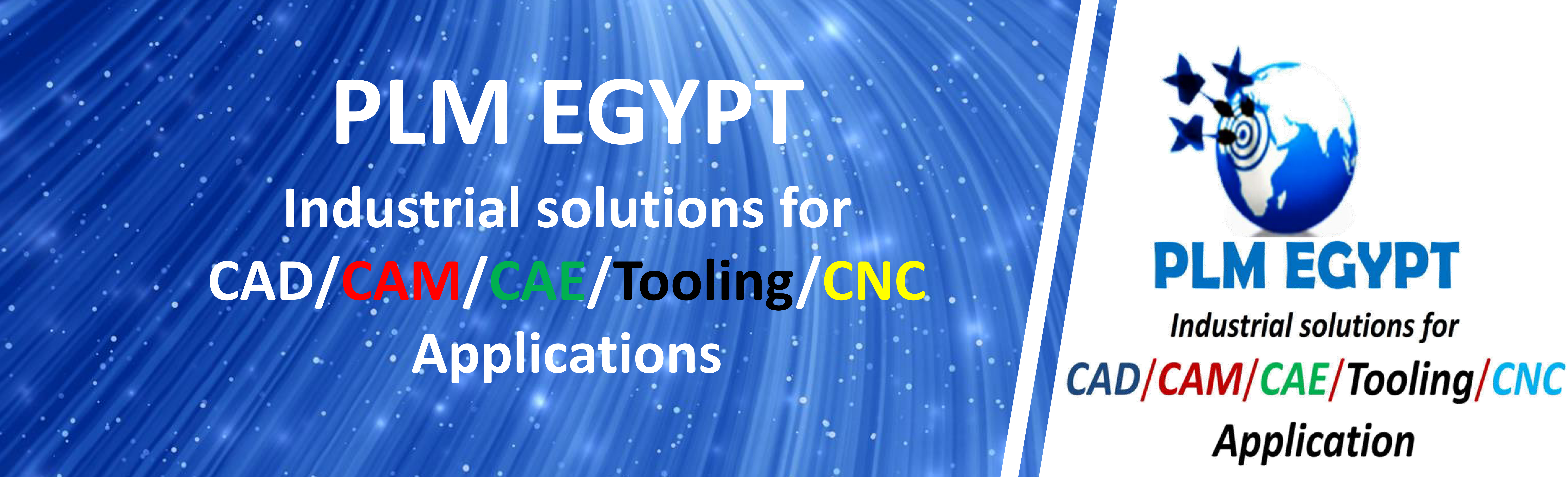
What is Moldex3D Plastic Molding
The leading true-3D molding simulation software can be applied in a wide range of plastic molding processes. We can predict potential manufacturing defects, validates part/mold design, lowers mold development costs, evaluates manufacturability, shortens time-to-market, and greatly increases business value.
- One single platform to run all powerful Moldex3D simulations
- Integrated workflow to ensure accurate meshing and modeling
- Support multiple processes by applications. Check out our solution
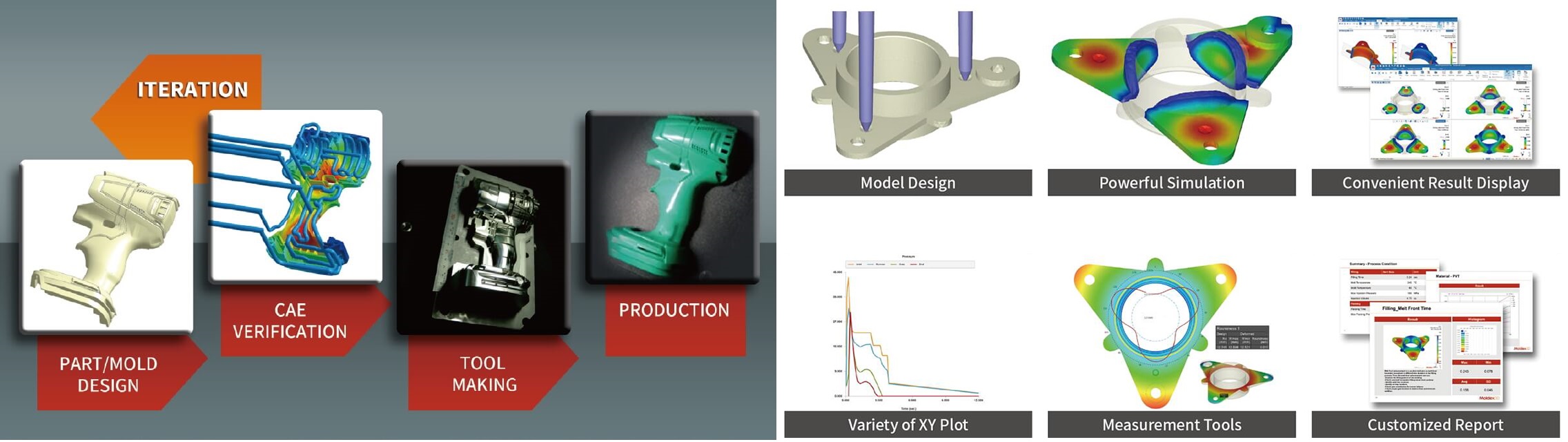
Why You Need Moldex3D
- Shorten cycle time and time-to-market
- Reduce number of mold trials and manufacturing costs
- Increase revenue and ROI
- Minimize product defects and extend mold life
Flow
- Predict melt front and flow patterns
- Optimize gate locations and designs
- Diagnose short shots, air traps, weld lines, flow imbalance, and more
- Simulate multi-component interaction
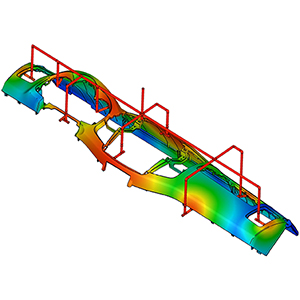
Pack
- Evaluate gate-freeze time
- Avoid sink mark or flash
- Optimize packing profile
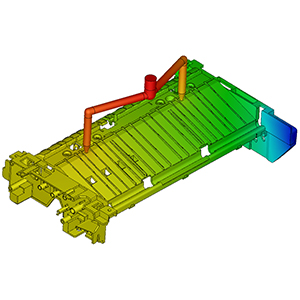
Cool
- Improve cooling efficiency and reduce cooling cycle
- Predict hot spots
- Support multiple cooling / heating system, conformal cooling and CFD
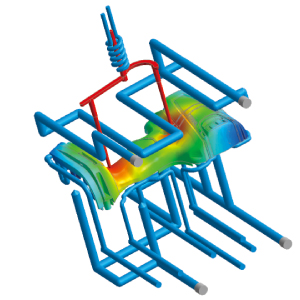
Warp
- Foresee final part shape
- Identify warpage causes
- Support residual stress, anisotropic, in-mold constraint effect analysis
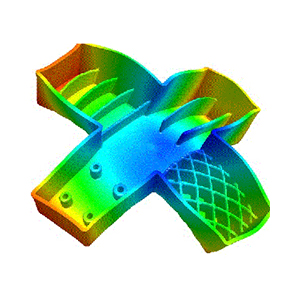
CAD & Mesh
- CAD conversion & repair tool
- Modeling Capability
- Powerful automatic & customized meshing technology
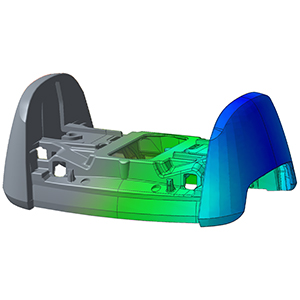
Advanced Analysis
- Machine Response & Plastification
- Advanced Hot Runner (AHR)
- Stress & Viscoelasticity (VE)
- Optics
- In-Mold Decoration (IMD)
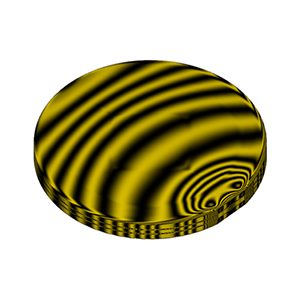
Computing
- Parallel Processing (PP)
- Remote computing
- Windows and Linux HPC platform supported
- Cloud-Connect: Cloud computing HPC toolkit
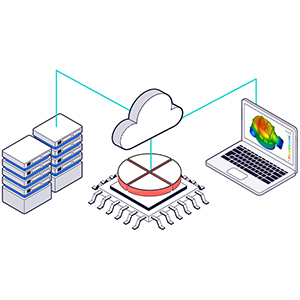
Automation
- Report Wizard
- Expert (DOE)
- Moldex3D API
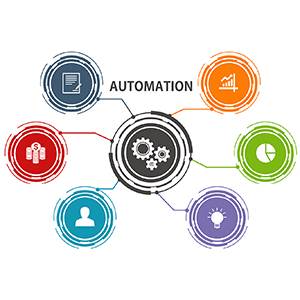
Solutions by Industry
Solutions by Application
Injection Molding
Foaming
Others
Moldex3D Solution Add-on
Expert (DOE)
helps users evaluate the optimal process conditions, such as packing time, cooling time, or mold temperature. Moldex3D Expert creates analysis variations and provides graphical summaries automatically.
SYNC
brings a simulation-driven design environment. With its powerful analysis capabilities fully embedded in mainstream CAD software, CAD users can synchronize design changes and quickly validate plastic designs.
Fiber Reinforced Plastics
Fiber
visualizes fiber orientation and calculates process-induced anisotropic thermo-mechanical properties for long and short fiber-reinforced plastics. Users can predict warpage distribution and evaluate part strength.
FEA Interface
provides a series of FEA Interface modules integrated with industrial leading structural software, including ABAQUS, Ansys, LS-DYNA, Marc, Nastran, and Radioss. Users can export Fiber and Stress analysis results to calculate further structural performance.
Micromechanics Interface
allows users to output more material properties for nonlinear multi-scale material modeling with integration of Digimat and Converse before FEA software.
Advanced Analysis
Stress
provides stress distribution for parts and part inserts. Users can set boundary conditions, such as stress or force, to evaluate the structure quality of plastics and predict potential breakage or deformation.
Viscoelasticity Viscoelasticity (VE)
calculates viscosity and elasticity variations of plastic materials under different temperature conditions. Users can evaluate the effects on molecular orientation, residual stress, warpage, and optical properties.
Advanced Hot Runner
visualizes the filling pattern and temperature distribution of hot runners and moldbase. Users can evaluate the heating efficiency and uniformity to optimize hot runner design.
Molding Processes
Compression Molding (CM)
simulates the compression molding process in which the polymer is squeezed into a preheated mold cavity. Moldex3D helps users check potential defects resulted from heat and pressure, decide appropriate materials, and optimize process conditions.
Injection Compression Molding (ICM)
Simulates the injection compression molding process, generally applied to thin and flat plastics, such as light guide plates or compact discs. Users can observe the compression process over time in cavity and evaluate material properties and process conditions.
Powder Injection Molding (PIM)
visualizes metal or ceramic molding process. Users can observe the fluid flow behavior of the feedstock, consisted of powder and binder, and predict potential defects. You also can evaluate the effects of shear rate and optimize process conditions.
Water-Assisted Injection Molding (WAIM)
visualizes the dynamics of water-assisted injection molding process for hollow plastics. With the visualization of fluid penetration behavior inside the mold cavity, users can define the overflow region and optimize process conditions.
Co-Injection Molding (CoIM)
visualizes the sequential injection molding process of skin and core plastic materials. Users can decide plastic material pair to optimize the combination of two material properties. You also can predict potential breakthrough on part surface.
Bi-Injection Molding (BiIM)
visualizes the molding process of two materials being injected independently into a mold cavity. Users can define material type, set independent filling and packing parameters for each material, and observe the flow rate variation from two melt entrances.